Cold Formed Parts for Manufacturing
What are Cold Formed Parts?
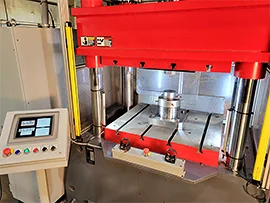
Cold Formed Parts are parts produced through processes known as cold heading, or impact extrusion, which are both types of cold forming. Cold forming is a manufacturing process, where a metal blank is shaped into a part by using various types of presses. This is a unique parts manufacturing process that results in no loss of material, which saves a significant amount of money. The basic cold forming process uses a simple metal blank that is cut from solid wire or bar stock, then placed in a punch and die set that is mounted on a vertical, mechanical or hydraulic press. Then the metal blank is simply pressed into the desired shape using extreme pressure. The mechanical force of the punch causes the metal to literally “flow” around the punch and take the shape of the die. Since this process is performed at room temperature, with no heat applied to the metal blank, the process is called “cold forming” and the parts produced are referred to as “cold formed parts.”
Deep impact extruded parts are produced using a type of cold forming (deep impact extrusion), which is used to produce parts with deep, hollow centers. Cold formed parts and extruded parts can be used to produce both low and high volume parts, as well as parts manufactured from higher cost materials such as copper, bronze, and aluminum. Cold formed parts deliver low-cost production advantages, and combined with our precision, secondary CNC machining, it allows our customers to achieve total part cost savings of 35% or more compared to conventional machining, with material cost savings of up 50% and machine cycle savings of over 60%.
What are the challenges of cold formed parts?
The challenges with cold formed parts are in how an engineer achieves the superior physical properties and high material cost savings benefits without spending thousands of dollars on the cold forming punch and die tooling? Before MFI, a standard cold formed part required high volume production in excess of 25,000 pieces in order to absorb the high costs of tooling and deliver the dual cold formed benefits of material savings and faster machining time.
What does MFI do that is unique with cold formed parts?
The standard cold formed part process requires production quantities from 25,000 to 100,000 pieces per year to absorb the high cost of cold formed tooling. At MFI, we use our internal tool manufacturing capabilities and quick-change tooling processes, to cost-effectively manufacture cold formed parts in production quantities as low as 1,000 pieces per year. Our cold formed parts process brings high volume production cost savings to our low volume customers.
What are the primary benefits of specialty cold formed parts compared to conventional machining from solid material?
- Raw material savings of up to 70%
- Reduced machining times up to 50%
- Improved mechanical properties for material strength and machining due to cold working of the material
- Significantly reduced total part costs up to 50%
Examples of Typical Cold Formed Parts
Cold formed parts are produced efficiently and cost-effectively for all types of manufacturing and a wide variety of parts. See our Gallery page for more examples of cold formed parts. Also, explore our website and learn more about the various types of extrusions used in making cold formed parts.
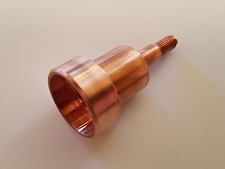
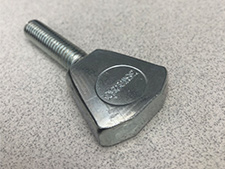
Contact us today to see how we can help your parts production and save you money with high quality Cold Formed Parts!
Watch Our Company Capabilities Video
Fill out our Inquiry Form for a Fast Response to your questions!