Specialty Cold Forming
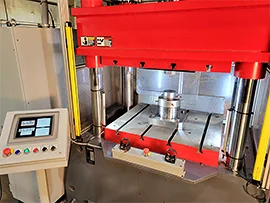
What is specialty cold forming?
Cold forming is a manufacturing process, where a metal blank is shaped by a punch and die set, using a vertical mechanical or hydraulic press, without loss of material. The basic cold forming process uses a simple metal blank that is cut from solid wire or solid bar, and placed in a punch and die set that is mounted on a vertical, mechanical or hydraulic press where the metal blank is pressed into the shape of the punch and die set. The mechanical force of the punch being driven into the die where the metal blank is contained causes the metal to flow around the punch and take the shape of the punch and die without loss of any of material. Because the metal forming process is done at room temperature and no heat is applied to the metal blank, the process is called cold forming.
Specialty cold forming uses the same basic cold forming process of punch and die metal forming, however it is focused on lower volume parts manufactured from higher cost materials such as copper, bronze, and aluminum. Our specialty cold forming delivers the low-cost production advantages of the cold forming process but at significantly lower production volumes. MFI's unique combination of its specialty cold forming process with precision, secondary CNC machining to manufacture low volume parts, allows our customers to achieve total part cost savings of 35% or more compared to conventional machining with material cost savings of up 50% and machine cycle savings of over 60%.
What are the challenges of specialty cold forming?
The challenges with specialty cold forming are how does an engineer achieve the superior physical properties and high material cost savings benefits of a cold formed part without spending thousands of dollars on the cold forming punch and die tooling? Before MFI, a standard cold forming process required high volume production in excess of 25,000 pieces in order to absorb the high costs of tooling in order to deliver the dual cold forming benefits of material content savings and faster machining time.
What does MFI do that is unique with specialty cold forming?
The standard cold forming process requires production quantities from 25,000 to 100,000 pieces per year to absorb the high cost of cold forming tooling. At MFI, we use our internal tool manufacturing capabilities and quick-change tooling processes, to cost-effectively manufacture specialty cold formed parts in production quantities as low as 1,000 pieces per year. Our specialty cold forming process brings high volume production cost savings to our low volume customers.
What are the primary benefits of specialty cold forming compared to conventional machining from solid material?
- Raw material savings of up to 70%
- Reduced machining times up to 50%
- Improved mechanical properties for material strength and machining due to cold working of the material
- Significantly reduced total part costs up to 50%
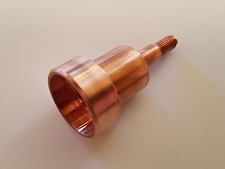
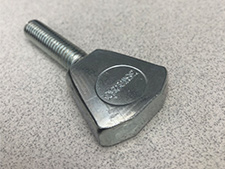